摘 要
本次设计内容为汽车刹车系统,其可靠性与驾驶人的生命息息相关,是汽车所有组成部分中最重要的一环。刹车系统是在车辆行驶过程中出现紧急情况时首先保护车辆与驾驶人员安全的反应系统,工作原理是依靠制动装置工作时产生的大量摩擦力来抵消车辆行驶时的动能,以达使车辆刹车减速,甚至停车静止的目的。现如今随着汽车技术和汽车动力的不断提高,对刹车系统的安全性和操纵性也提出了更高的要求。
本次设计主要围绕汽车刹车系统的结构来进行设计,对刹车系统的主要组成零部件进行方案优化分析。对刹车系统每一个组成部分都单独进行了计算,最后汇总主要参数信息,如汽车的制动力矩、制动主缸的直径、鼓式制动器的设计参数、制动器的相关参数、制动轮缸的工作容积以及制动踏板力与踏板工作路程的关联性计算等来进行汽车整体设计分析,设计出一款造价费用较低,性能稳定的刹车系统。合理运用辅助设计软件CATIA建立三维模型,对以设计好的的三维模型进行检验,避免零部件干涉等问题,经检验合格后,将设计合理的模型图输出成二维工程图。参照本次设计的装配和零部件图纸,可以更容易地理解此次设计的汽车刹车系统的布置以及思想。最终,根据设计的模型图来制作实物原理模型。
关键词:刹车系统; 制动器; 制动力矩; 三维建模
1 设计方案
1.1 制动系统的分类
按照工作时功用可分为:
(1)行车制动系统;
(2)驻车制动系统;
(3)应急制动系统;
(4)辅助制动系统。
按照制动能源可分为:
(1)人力制动系统—完全依赖司机的自我动能;
(2)动力制动系统—将发动机工作时产生的热能和动能转变为其他形式的能量对汽车进行安全制动;
(3)伺服制动系统—兼用人力和发动机的动能进行制动的制动系统。
按照能量的传输方式可分为:
(1)机械式;
(2)液压式;
(3)气压式;
(4)电磁式。
本次设计的出发点是让汽车能更好地在一般道路下行驶,而不是在山区等特殊路况下行驶,因此对辅助制动系统不进行深入研究。另外,考虑到本次设计所需费用的问题,故用所设计的驻车系统来取代应急系统,所以本次设计主要对制动系统和驻车制动系统来进行优化改进。
3.2 产品结构设计
汽车刹车系统的结构主要有10个部分组成,它们分别是制动踏板和手柄、制动鼓、制动盘、汽车制动底板、制动摩擦衬片、制动蹄、制动钳,制动轮缸等。如图3.1所示。
图3.1 制动系统主要结构
(1) 制动踏板和手柄
根据人体工程力学的要求对汽车刹车踏板的行程和手动制动杆的位置进行设计,要求既要方便驾驶人操纵,还要尽可能提高驾驶舒适性。踏板行程:对轻型汽车来说应小于165mm,其中考虑了摩擦衬片的容许磨损量。手动制动杆的工作行程不应超过175mm~220mm。参照汽车行业规定,汽车制动踏板作用力一般为400N(轿车)—600N(货车)。
(2) 制动鼓
高刚性和高的热容量可以说是汽车制动鼓必须具备的条件,这将确保制动鼓在汽车制动器经常工作时也不超过温度极限,并且制动鼓也具有高的摩擦系数。轻型,中型和中型卡车,公共汽车经常使用HT200灰铸铁或合金铸铁制动鼓(图3.2的(a));市场上大多数的汽车使用钢板冲压滚筒的圆筒部腹板灰口铸铁的组合制动鼓整体铸造(图3.2(b))。内鼓筒是灰铸铁加工而成的铸铝合金制动鼓(图3.2©)在汽车市场中也占有很大一部分比例[11]。
图3.2 制动鼓
根据刚性和强度的制动鼓的壁厚选择,当初认为有助于提高采取更大的壁厚的热容量似乎是一个不错的选择,但实验表明,即使在厚度13毫米增加到22毫米,最高摩擦表面温度不会有太大的变化。因此,在一般的制动鼓的铸件的壁厚被选择为:轿厢8〜13毫米,中型,大型客车是14〜19毫米。
2 三维建模
本次三维建模均采取CATIA软件进行绘制,对于标准件则直接在CATIA软件的重用库里进行调取,最后对零件的三维建模进行了装配。
2.1 制动器主要零部件建模
2.1.1 后遮污板
以xy基准面为草图平面,先在xy基准面绘制一个直径为120.5mm的大圆,在绘制一个直径100mm的小圆,保存草图。
图4.1 草图平面
2.2 其它重要零部件
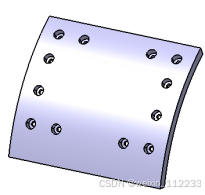
图4.12 摩擦衬片
图4.13 支撑销
3 前后装配图
图4.18 前轴装配图
图4.19 后桥装配图
4 整体渲染
之前已经对汽车刹车系统零部件建立了三维模型,但是三维模型图整体颜色较为统一,不能有效展示整体外观,为了更好地展示汽车零部件外观,需要对刹车系统零件的三维模型图进行渲染,尽可能的接近实际生产情况。
汽车刹车系统零部件的三维模型是采用CATIA软件绘制的,由于CATIA软件的渲染效果较差,为了更好地美化三维模型,本次采用Keyshot软件对产品整体进行渲染。
首先,先在CATIA软件中将整体模型导出至Parasolid文本文件,导出的文件格式后缀为x-t。打开Keyshot软件,导入之前导出的X-T文件,然后对模型进行渲染,导入的模型软件将默认为统一材质和颜色,我们在渲染时,要首先对渲染的部件进行解除材料链接,再对部件进行材料赋予,然后改变部件颜色,调整渲染文件的各种场景、灯光等要素,达到较好的显示效果,再渲染成图片。最终得到的效果图如图所示。
图6.1 三维装配渲染图
5 实物制作
鉴于材料、成本等因素,汽车刹车系统设计方案完成后,产品实物则需要用3D打印设备进行制作。
3D打印设备的原理就是把数据和原料放进3D打印机中,机器会按照程序把产品一层层制造出来。
3D打印技术已经较为成熟,能够较为清晰的展示最终的整体模型效果,但是由于汽车刹车系统的整体模型尺寸较大,综合考虑展示效果以及成本问题,在打印时要进行整体模型进行缩放,在打印时可以适当地对缩放模型进行修改,最好修改部位在整体内部进行,不得改变整体外形尺寸,具体实施方案如:适当加厚某个部位板材的厚度,也可以在内部打印支撑柱的形式进行。
图7.1 实物模型
6 结 论
本文设计的汽车刹车系统,确定了符合标准的制动方案,同时结构合理,可保证汽车在刹车时能够受力平衡,而且使驾驶人的安全得到保障,拥有良好的工艺性能和工作效率。
本次设计首先介绍了制动系统的发展现状,并对制动系统的作用,工作原理及分类进行了简要分析说明,并结合我国现有的相关标准和法规,应用汽车制动理论,对汽车刹车系统进行合理的设计和有限元分析。设计过程中,参照国家法律法规以及相关标准对所设计的各零部件进行校核分析,满足市场相关要求。
尤其是对汽车刹车系统的组成以及各部件的结构进行了严密的理论证明,对工程设计的方法进行了摸索与实践,实现了设计任务的要求。通过这些设计和计算,运用软件合理绘制汽车刹车系统的三维模型和二维图纸,最后产品的实际效果与设计思路完全一致,完成了汽车刹车系统的设计。