一、BMS技术简介
在全球碳中和目标的战略驱动下,新能源汽车产业正以指数级速度重塑交通出行格局。动力电池作为电动汽车的"心脏",其性能与安全性不仅直接决定了车辆的续航里程、使用寿命等关键指标,更深刻影响着消费者对电动汽车的市场接受度。
而电池管理系统(Battery Management System, BMS)是动力电池安全运行与性能释放的核心技术支撑。
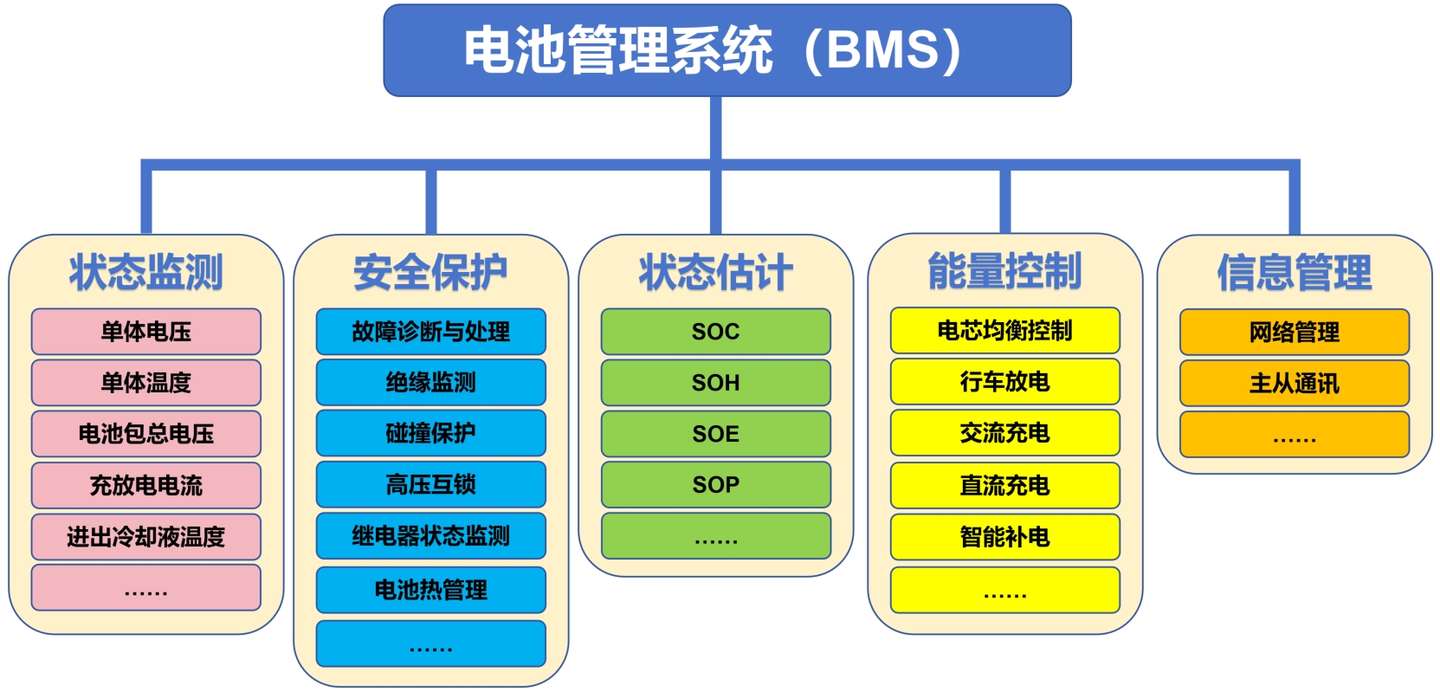
BMS用于监控、管理和保护电动汽车动力电池组,其主要功能包括实时采集电池的电压、电流、温度等参数,评估荷电状态(SOC)、健康状态(SOH)等,并通过均衡管理、热管理及安全保护策略延长电池寿命,确保安全运行。
BMS的典型拓扑结构主要分为集中式和分布式两种。在汽车行业中,分布式架构BMS因其良好的可扩展性和模块化设计而被广泛采用,其技术架构如图所示(图片参考:Blommy)。
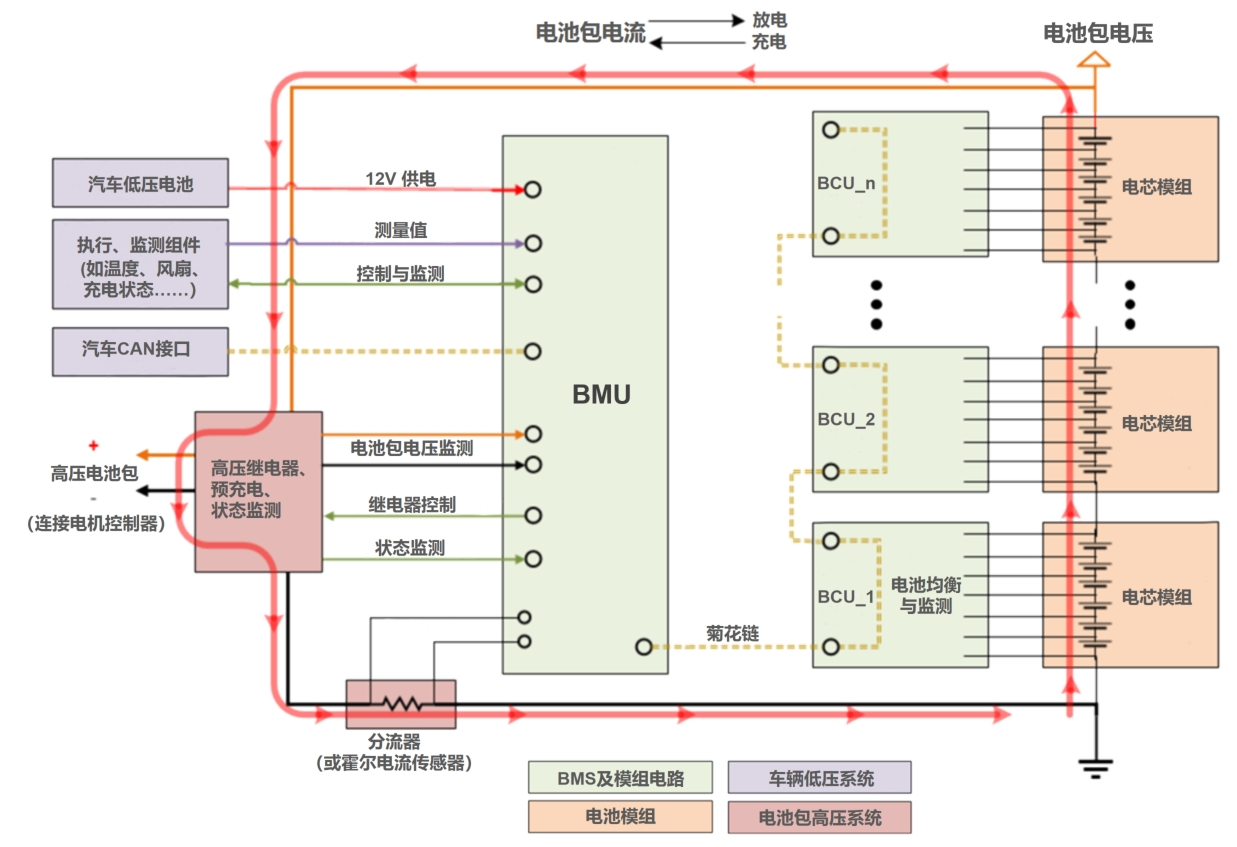
在该架构中,BCU(从板模块)直接与各电池单体连接,负责采集电池单体的电压、温度等关键参数信息,同时执行电池均衡控制。各BCU通过先进的总线通信技术将采集到的电压、温度等数据传输至BMU(主板模块),其中SPI菊花链通信和CAN通信是目前行业内主流的两种总线技术方案。
BMU通过专用接口及总线系统获取这些必要信息,并基于预设的算法模型实现电池状态估算、故障诊断及安全管理等核心功能。
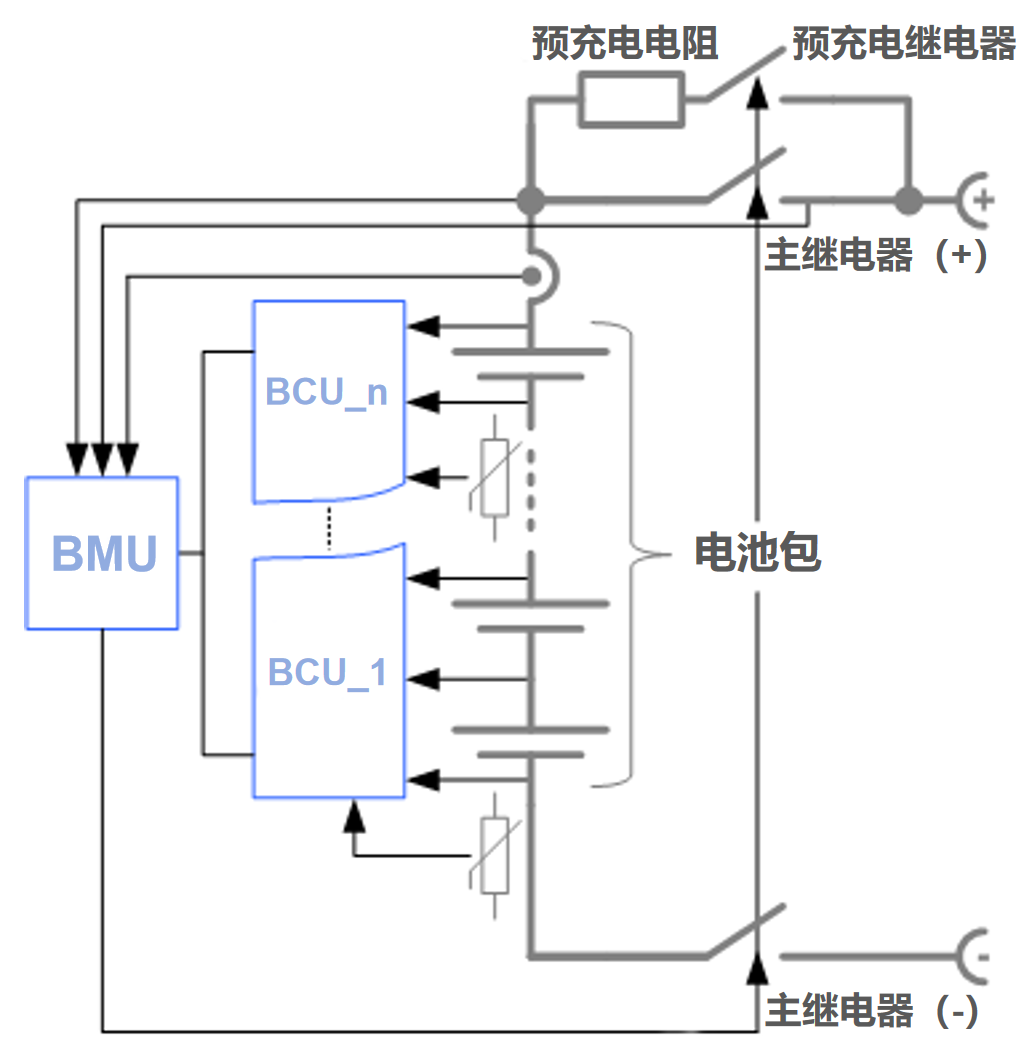
目前BMS系统的发展趋势:
智能化升级:AI驱动的SOH估算误差可降至3%以内,并支持寿命预测。
无线BMS:采用蓝牙或Wi-Fi减少线束复杂度,特斯拉、通用、宝马等车企均已开始相关布局。
固态电池适配:针对固态电池低内阻特性开发新型均衡策略与热管理方案。
域控化整合:动力域控制器集成BMS、电机控制等功能。
二、HIL测试的必要性
BMS性能直接影响动力电池能量利用率和寿命,是决定电动汽车安全性和续航里程的核心技术,随着电池能量密度提升、快充技术迭代和极端工况需求增长,BMS的复杂性也呈几何级数攀升。在《电动道路车辆安全规范》框架下,电池管理系统(BMS)需同时满足功能安全、热失控防护及网络信息安全三重技术规范。
在传统开发模式下,电池管理系统(BMS)的验证工作面临诸多挑战,这些因素(如下所示)共同制约了BMS验证的效率和可靠性。
挑战与制约因素:
1 |
测试验证效率较低,难以满足快速迭代的开发需求; |
2 |
极限工况的覆盖存在较大困难,无法全面模拟各种极端场景; |
3 |
隐性缺陷的追溯问题突出,软件逻辑漏洞或硬件兼容性问题往往在后期才被发现; |
4 |
研发成本持续攀升,测试所需资源和设备投入巨大。 |
HIL(硬件在环测试)技术的突破性应用,为BMS开发开启了数字孪生新时代。通过构建高精度电池模型与实时仿真环境,工程师可在实验室中即可完成全生命周期、全工况场景的闭环验证,并通过自动化测试,实现科学、全面、重复的BMS功能测试,提升BMS控制策略验证效率、缩短开发周期、降低测试成本、提前识别并拦截失效风险。
当前,全球顶尖车企与Tier1供应商正加速布局BMS HIL测试体系,以此提升算法迭代速度、提升算法精度、提升测试效率、提升产品良品率。这场"虚拟验证革命"不仅重新定义了动力电池开发流程,更铸就了智能电动汽车时代的核心竞争力壁垒。
三、BMS HIL测试系统
1、系统架构
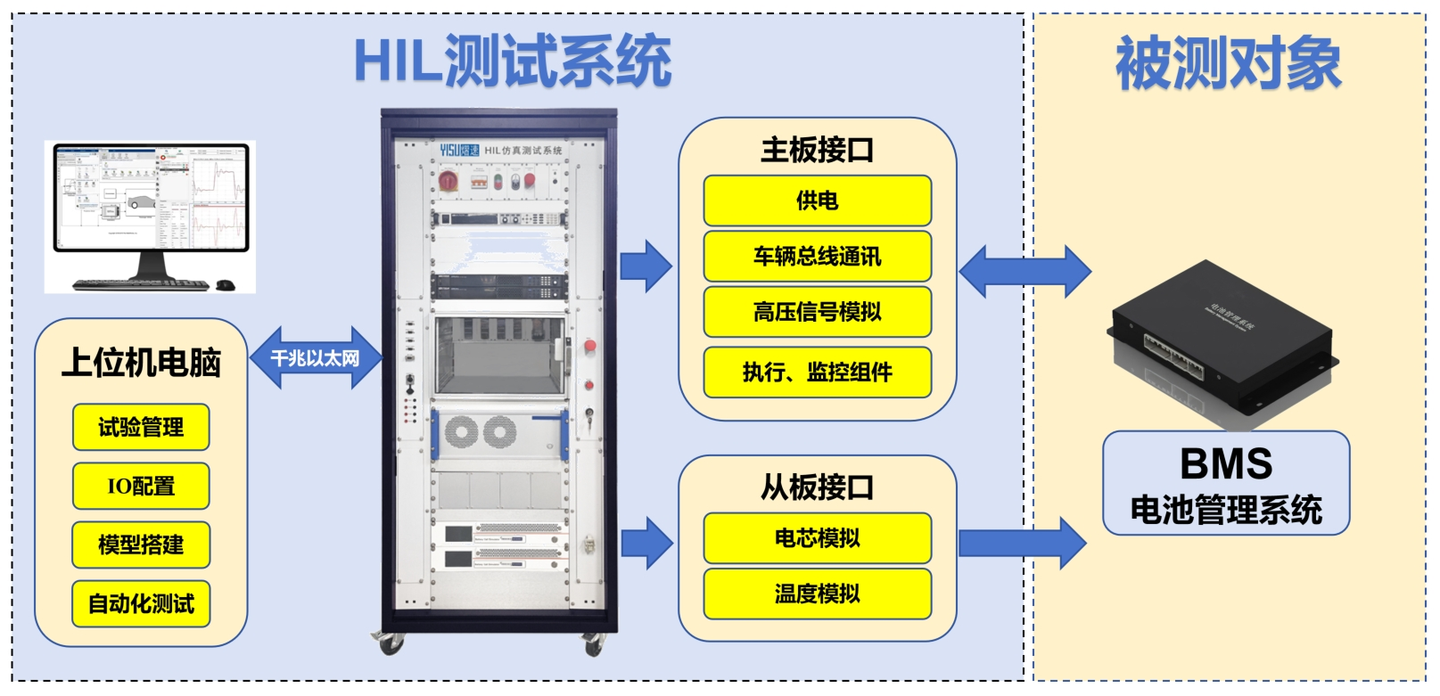
如图所示,BMS HIL测试系统主要包括以下三部分:
① 上位机
开发和编译电池实时仿真模型;
通过试验管理软件,搭建上位机界面,实现实时在线调参、波形显示、数据记录等操作;
通过自动化测试软件,开发测试用例,一键测试执行,并输出测试报告。
② 实时仿真系统
包括实时系统、通用IO系统、高压负载仿真组件、故障注入系统、电池模拟器等等。
③ 被测控制器
待测的BMS电池管理系统。
主板接口实现:
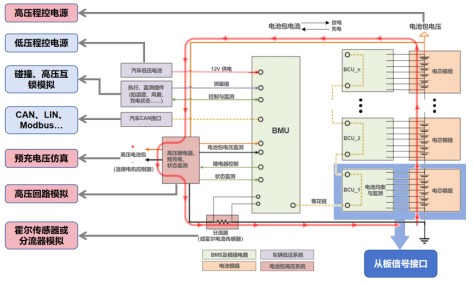
从板接口实现:
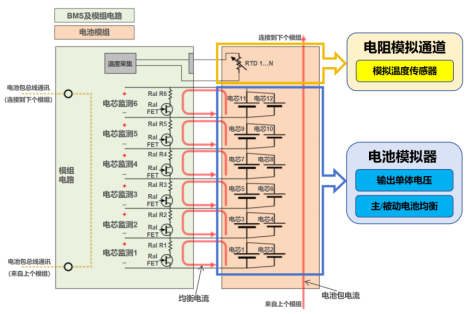
2、电池模拟器
PolarCell电池单体模拟器专为电池管理系统(BMS)的全生命周期测试设计,服务于新能源汽车、储能系统及可再生能源领域。该设备通过高精度电压模拟,结合实时仿真模型,可真实复现电池单体的动态特性,支持BMS硬件在环(HIL)测试、验证测试(DV)及下线测试(EOL)。
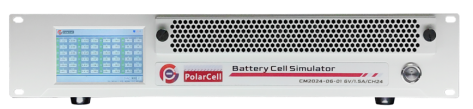
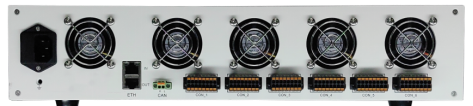
PolarCell采用EtherCAT实时通讯协议,可在1ms内实现200+通道同步更新,满足复杂工况下对响应速度的严苛需求。其模块化设计整合了紧凑型结构与多重散热方案,配合可替换防尘棉,确保了设备在密集使用环境中的稳定性。此外,用户也可通过触摸屏或CAN总线直接控制各通道输出,简化了操作流程。
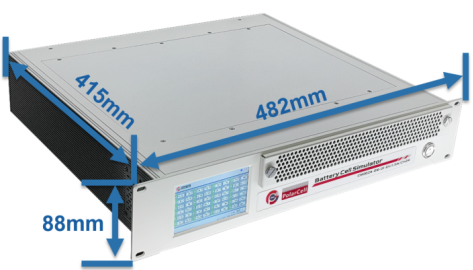
该模拟器支持主动双向电流控制模式,可灵活限制电流范围,适应充放电测试及休眠电流检测等场景。独特的通道并联功能无需硬件改动即可提升输出能力,解决了大电流测试需求与系统成本间的矛盾。
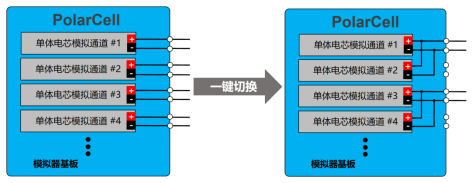
此外,PolarCell内置故障注入机制,可模拟电池单体开路、短路、极性反转等异常状态,为BMS安全策略验证提供完整测试环境。
在安全防护方面,PolarCell集成过压、过流、过温三重保护策略,满足车企与Tier 1供应商对测试平台安全性的要求。
总而言之,作为BMS HIL测试系统的核心设备,PolarCell通过实验室环境下的全工况模拟,显著缩短了产品开发周期,成为动力电池安全技术迭代的关键工具。
3、仿真模型
01 电池模型
电池模型
电池模型基于 3阶RC等效电路模型搭建,电池模型可精确模拟电池单体及电池包的工作特性。其详细信息如下:
①建模环境
基于MATLAB/Simulink平台进行系统建模与仿真;
提供基础功能性模型和精确物理外特性动态模型。
②电特性模拟
实时模拟SOC、温度、充放电电流对电池电压的影响;
支持电池串联、并联等多种拓扑结构的仿真;
可监测任意单体电压、电池总成电压及输出电流;
支持外接充电与能量回收充电过程的模拟。
③热特性模拟
模拟单体间的温度差异及其变化;
支持BMS风扇、水泵控制信号的响应与特性模拟。
④故障模拟
可模拟SOC过高/过低等极端工况
支持电池过流故障的仿真
可实现母排过压故障的仿真
02 充电桩模型
充电桩模型符合国家标准GB/T 27930和GB/T 18487,具备高度兼容性与功能性。其中,直流充电桩模型可以通过J1939协议实现与BMS控制器的直接总线报文交互。
此外,我们还基于ISO 61851、SAE J1772和ISO 15118等协议开发了EVSE仿真模型,配合专用的欧美标充电插枪仿真模块,实现了CP信号仿真、PLC通讯仿真以及充电逻辑仿真等功能。
快充模型能够根据BMS控制器的需求动态调整电压与电流,并精准提供CC2充电枪连接信号及充电接口温度监测功能;慢充模型能够提供CC、CP等慢充信号,并根据BMS需求灵活调节输出电压与电流,CC、CP信号可根据充电状态动态调整响应数据,确保充电过程的精确控制与高效运行。
此外,模型可以轻松模拟充电机故障场景,有效验证BMS控制器的充电逻辑,并自动记录完整通讯数据,生成测试报告。
03 虚拟控制器模型
各类虚拟控制器模型需要根据待测车型的拓扑结构及控制器功能进行定制化开发,涵盖电机控制器(MCU)、整车控制器(VCU)、直流-直流变换器(DC-DC)等关键部件。
这些模型可集成到BMS(电池管理系统)HIL测试系统中,实现多控制系统的网络化协同测试,从而全面验证整车级功能与性能。
得益于多年来在仿真测试领域的项目实施经验与技术沉淀,熠速组建了一支经验丰富的专业模型开发团队,能够为客户提供高效、精准的定制化开发服务,确保虚拟控制器模型的高保真度与实时性,助力缩短开发周期并降低测试成本。